Research
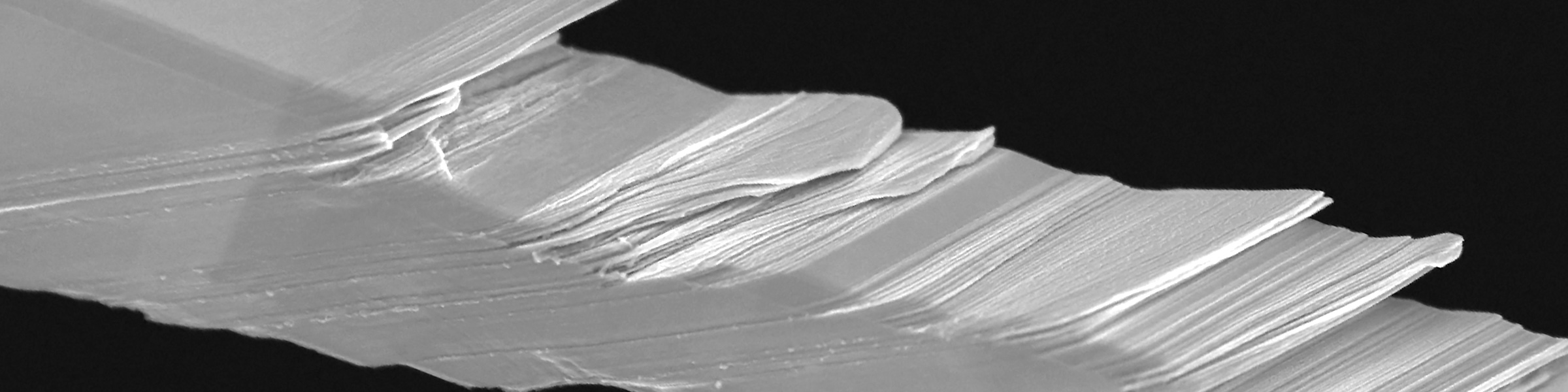
Exploring the unknown mechanical and physical properties of nano- and micro-sized materials.
It is known that materials exhibit specific properties much different from those of the bulk (macro-sized materials) when their dimensions are shrunk down to nanometer- to micrometer-scale.
In this laboratory, we conduct mechanical loading experiments on nano- and micro-sized structures in various microscopes (transmission electron microscope, scanning electron microscope, atomic force microscope, piezoelectric response microscope, magnetic force microscope) and investigate the strength and fracture properties with the assistance of computational and theoretical analysis. In addition, we carry out research to elucidate the coupling effects (multiphysics properties) between various physical properties (ferroelectricity, magnetism, etc.) of nanostructured materials and their mechanical characteristics. In addition, we are also interested in mechanical metamaterials that have specific internal structures and exhibit mechanical properties that are not possible with conventional materials.
Research Themes
Research on fatigue behavior of nano- to micro-sized metals
Metal fatigue is the most common cause of failure in structures. For metals, fatigue cracks are generated by the formation of characteristic fatigue dislocation structures. The size of these structures is a few micrometers, which is independent of the material dimensions. This implies that this conventional fatigue dislocation structures cannot exist inside nano- and micro-sized materials. In other words, there is a possibility that nano- and micro-sized materials have a unique fatigue behavior. We conduct fatigue tests and detailed observations in transmission and scanning electron microscopes in order to clarify this. We have the world's leading technology for fatigue testing of nano- and micro-sized materials.
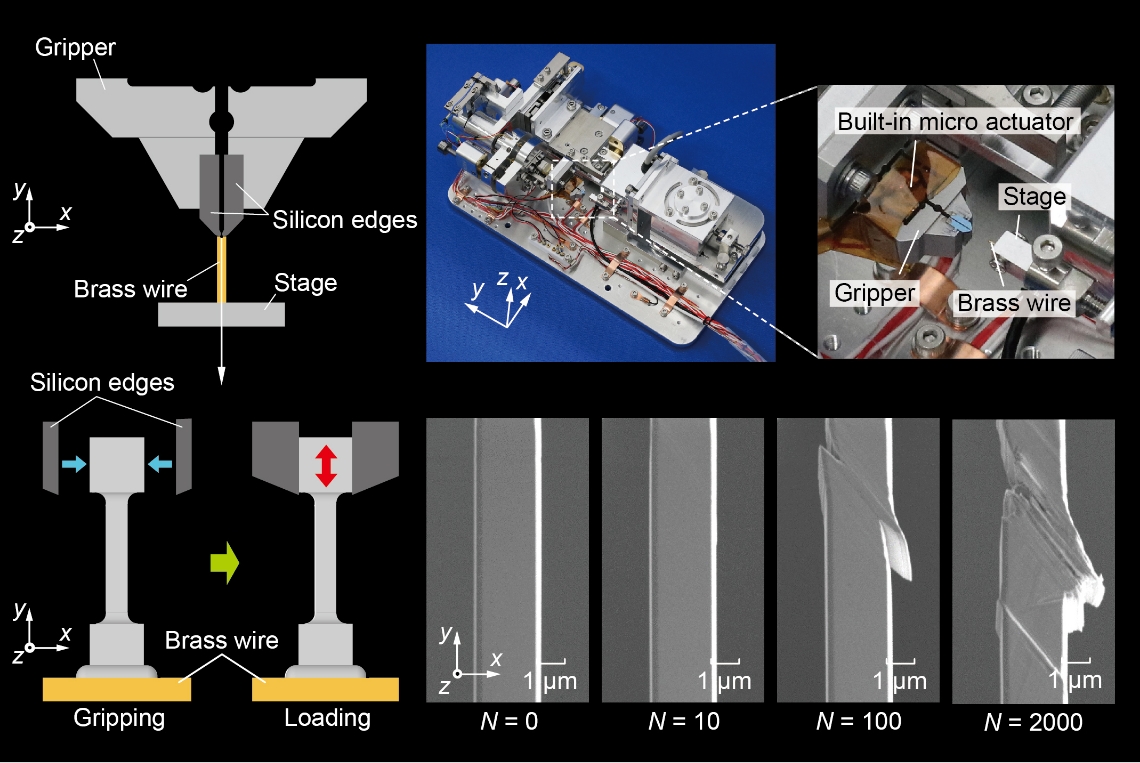
Related Videos
Tension and Compression Cyclic Loading Test on Micro-sized Single Crystal Copper
In situ observation on formation process of nanoscale cracking during tension-compression fatigue of single crystal copper micron-scale specimen
Takashi Sumigawa, Kim Byungwoon, Yuki Mizuno, Takuma Morimura, and Takayuki Kitamura
Acta Materialia, Vol. 153 (2018) pp. 270-278.
DOI: https://doi.org/10.1016/j.actamat.2018.04.061
Tension and Compression Fatigue Test on Micro-sized Single Crystal Copper
FE-SEM in situ observation of damage evolution in tension-compression fatigue of micro-sized single-crystal copper
Takashi Sumigawa, Shin Uegaki, Tetsuya Yukishita, Shigeo Arai, Yoshimasa Takahashi, and Takayuki Kitamura
Materials Science and Engineering A, Vol. A 764 (2019) 138218.
DOI: https://doi.org/10.1016/j.msea.2019.138218
Interfacial Fatigue Cracking in Nanomaterial with Stacked Structure
Cu/Si Interface Fracture due to Fatigue of Copper Film in Nanometer Scale
Takashi Sumigawa, Tadashi Murakami, Tetsuya Shishido, and Takayuki Kitamura
Material Science and Engineering A, Vol. 527 (2010) pp. 6518-6523.
DOI: 10.1016/j.msea.2010.07.002
Research on multiphysics properties of materials
In this age of rapid development and evolution of nanotechnology, it is no exaggeration to say that the social infrastructure of humankind is supported by the unique functions of nano-sized materials. Although nano-sized materials have different properties from macromaterials (bulk) due to the significant surface effects, the details of their mechanical responses to various physical properties have not been clarified. Therefore, we are studying the responses of nano-sized materials under mechanical loading, focusing on ferroelectricity, magnetism, Mott transition, and so on. We have the observation equipment (transmission electron microscope, piezoelectric response microscope and magnetic force microscope) necessary for this research, and elucidate the phenomena using loading equipment we developed originally.
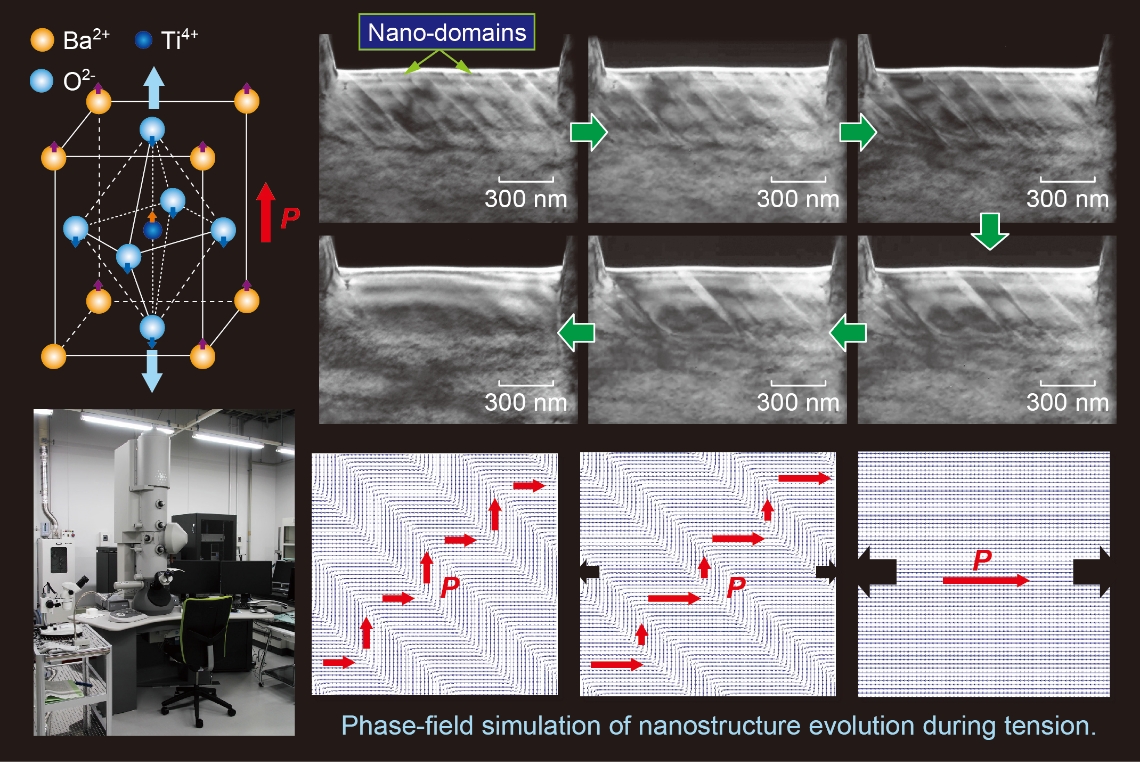
Related Videos
Pre-crack introduction into silicon single-crystal specimen
Fracture Toughness of Silicon in Nanometer-scale Singular Stress Field
Takashi Sumigawa, Shinsaku Ashida, Shuhei Tanaka, Kazunori Sanada, and Takayuki Kitamura
Engineering Fracture Mechanics, Vol. 150 (2015) pp. 161–167.
doi:10.1016/j.engfracmech.2015.05.054
Crack propagation test from nano-sized singular stress field - 1
Fracture Toughness of Silicon in Nanometer-scale Singular Stress Field
Takashi Sumigawa, Shinsaku Ashida, Shuhei Tanaka, Kazunori Sanada, and Takayuki Kitamura
Engineering Fracture Mechanics, Vol. 150 (2015) pp. 161–167.
doi:10.1016/j.engfracmech.2015.05.054
Crack propagation test from nano-sized singular stress field - 2
Griffith Criterion for Nanoscale Stress Singularity in Brittle Silicon
Takashi Sumigawa, Takahiro Shimada, Shuhei Tanaka, Hiroki Unno, Naoki Ozaki, Shinsaku Ashida, and Takayuki Kitamura
ACS Nano, Vol. 11 (6) (2017), pp. 6271–6276.
http://pubs.acs.org/doi/abs/10.1021/acsnano.7b02493
Fracture Test from the Interface Edge of Nanomaterial with Stacked Structure
Interface Crack Initiation due to Nanoscale Stress Concentration
Takashi Sumigawa, Tetsuya Shishido, Tadashi Murakami, and Takayuki Kitamura
Material Science and Engineering A, Vol. 527, No. 18-19 (2010) pp. 4796-4803.
DOI: 10.1016/j.msea.2010.04.002
Fracture Test from the Center of the Interface of Nanomaterial with Stacked Structure
Interface Crack Initiation due to Nanoscale Stress Concentration
Takashi Sumigawa, Tetsuya Shishido, Tadashi Murakami, and Takayuki Kitamura
Material Science and Engineering A, Vol. 527, No. 18-19 (2010) pp. 4796-4803.
DOI: 10.1016/j.msea.2010.04.002
Mixed-mode Crack Initiation at the Edge of the Interface of Nanomaterial with Stacked Structure
Mixed-mode crack initiation at the edge of Cu/Si interface due to nanoscale stress concentration
Kohei Kishimoto, Yabin Yan, Takashi Sumigawa, Takayuki Kitamura
Engineering Fracture Mechanics, Vol. 96 (2012) pp. 72-81.
DOI: 10.1016/j.engfracmech.2012.07.027
Interfacial Crack Initiation Tests in Nanomaterial with a Notch - 1
Fracture Mechanics Investigation on Crack Propagation in the Nano-multilayered Materials
Licheng Guo, Takayuki Kitamura, Yabin Yan, Takashi Sumigawa, Kai Huang
International Journal of Solids and Structures, Vol. 64–65 (2015) pp. 208–220.
DOI: 10.1016/j.ijsolstr.2015.03.025
Interfacial Crack Initiation Tests in Nanomaterial with a Notch - 2
Fracture Mechanics Investigation on Crack Propagation in the Nano-multilayered Materials
Licheng Guo, Takayuki Kitamura, Yabin Yan, Takashi Sumigawa, Kai Huang
International Journal of Solids and Structures, Vol. 64–65 (2015) pp. 208–220.
DOI: 10.1016/j.ijsolstr.2015.03.025
Research on mechanical metamaterials
By making controlled artificial structures in materials, we can create "metamaterials" (materials beyond materials) with physical properties that do not appear in materials in nature. Today, it is possible to make metamaterials with nano- and micro-sized structures. On the other hand, it is necessary to investigate structures that exhibit new mechanical properties prior to the miniaturization of structures. Therefore, we design metamaterials that express characteristic mechanical properties (mechanical metamaterials), actually fabricate them using a 3D printer, and demonstrate their deformation and fracture behavior through experiments.
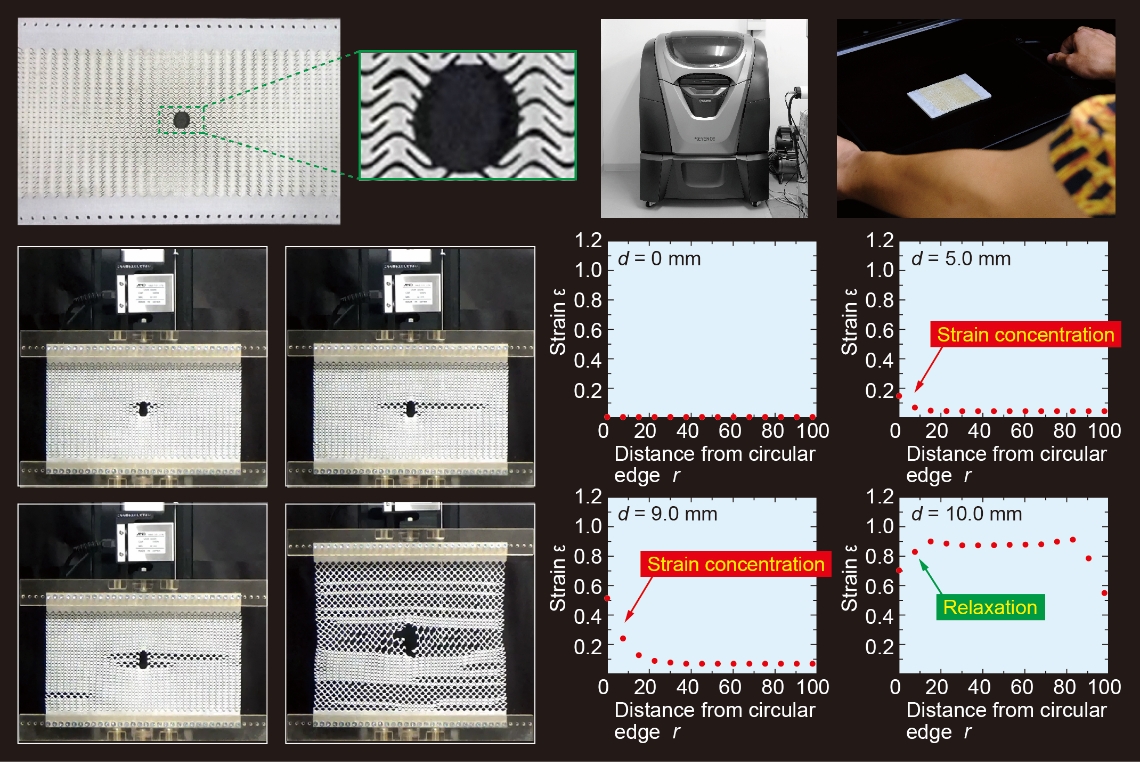
Research on elucidation of mechanical governing factors for nano-scale fracture
At a crack tip, there is a singular stress field in which the stress increases to infinity. The singular stress field also occurs at the junction between the interface of dissimilar materials and the free surface. Fracture phenomena in materials have conventionally been discussed using the mechanics of fracture under the continuum assumption (fracture mechanics), but when the material dimensions are reduced to the nanoscale, the singular stress field is reduced to an equivalent size by the similarity law. In this case, the number of atoms contained in this region is about several tens, and it is not clear whether the discussion under the continuum assumption is possible or not. We are trying to elucidate this experimentally and analytically. Recently, we have succeeded for the first time in the world in conducting fracture experiments from atomic-level line defects (dislocations) and clarifying fracture phenomena from atom-sized singular stress fields.
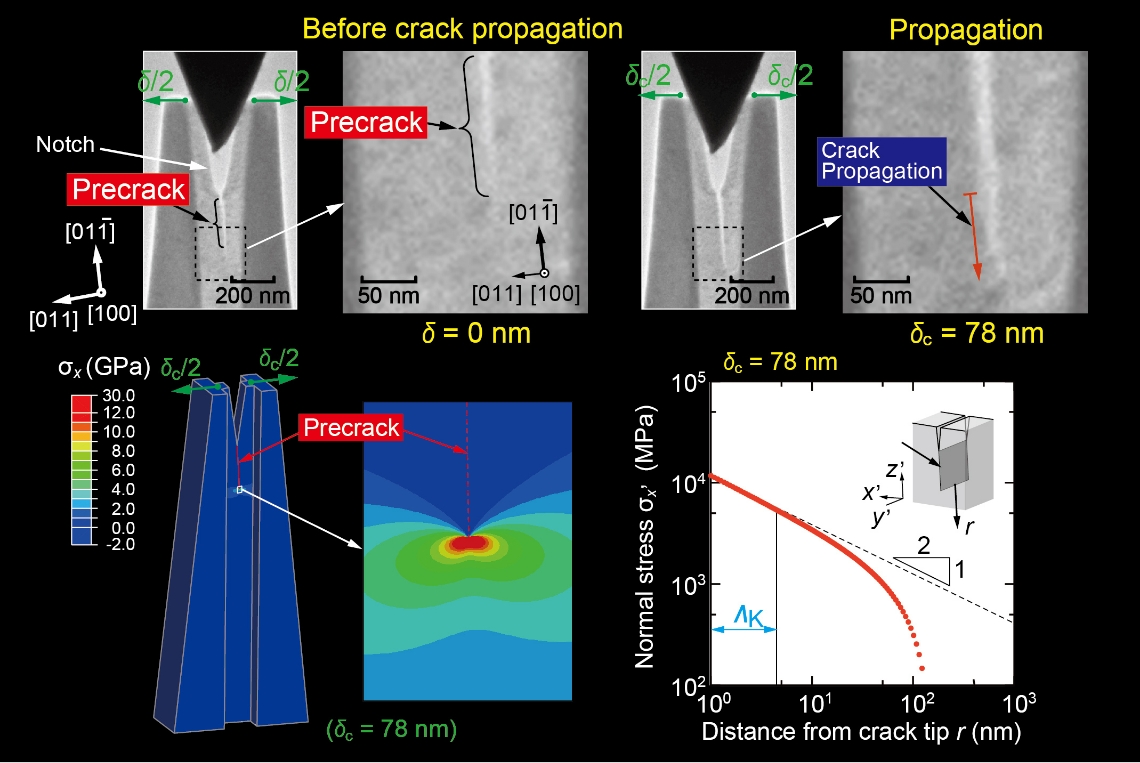
Related Videos